
The Packsize X5, the world’s first fully-automated erected box system. | Courtesy of Packsize
Companies Make Headlines with Small Footprints, High Speeds
These companies made headlines in 2023 for offering equipment with faster run rates and greater efficiency while taking up less floor space.
Packaging equipment witnessed a plethora of innovations in 2023, and this definitely applies to case forming, packing and sealing.
Some of the innovations were award-winning. Packsize was nominated for – and was the recipient of – several awards for its X5® solution, which it touts as “the world’s first fully-automated erected box system” and “the most advanced, flexible, efficient and sustainable platform available for the e-commerce industry.”
In May, MGS announced the release of its new Matrix TL top-loading case packer. Ideal for packaging facilities with low-to-medium production rate requirements and diverse packaging requirements, the Matrix TL offers a complete form, fill and seal case packing solution with a small footprint, competitive rate of speed and quick changeovers.
Not to be outdone, Ishida Europe announced in September the launch of a new version of its ACP-700 series automatic case packing system (ACP) for snacks and other dry product packs, offering a fast, flexible and highly compact solution for a wide range of bag and case sizes and pack patterns.
The ACP-722 RRP offers one of the smallest footprints currently available, being up to 50% smaller than equivalent casepacker models.
Read more about these game-changing innovations!
Packsize's X5 Erected Box System Named Finalist for 2023 MHI Innovation Award
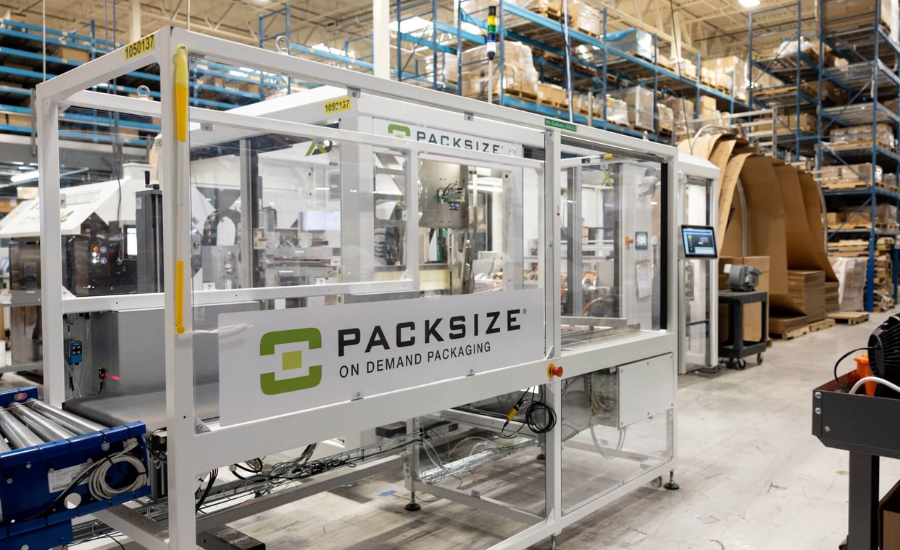
The Packsize X5 solution produces ready-to-pack, right-sized erected boxes at an industry-leading speed of up to 600 boxes per hour. Courtesy of Packsize
Packsize®, the market leader in sustainable, right-sized, on-demand packaging, announced in March that its new X5® solution is a finalist for the 2023 MHI Innovation Award for Best New Innovation. The X5 is the world’s first fully-automated erected box system and the most advanced, flexible, efficient and sustainable platform available for the e-commerce industry.
While the X5 ultimately was not chosen as the MHI winner, it was selected as a Materials Handling News 2023 Readers' Choice Product of the Year, and it was named 2023 Top Software & Tech by Food Logistics and Supply & Demand Chain Executive.
MGS introduces compact top load case packer for diverse packaging requirements
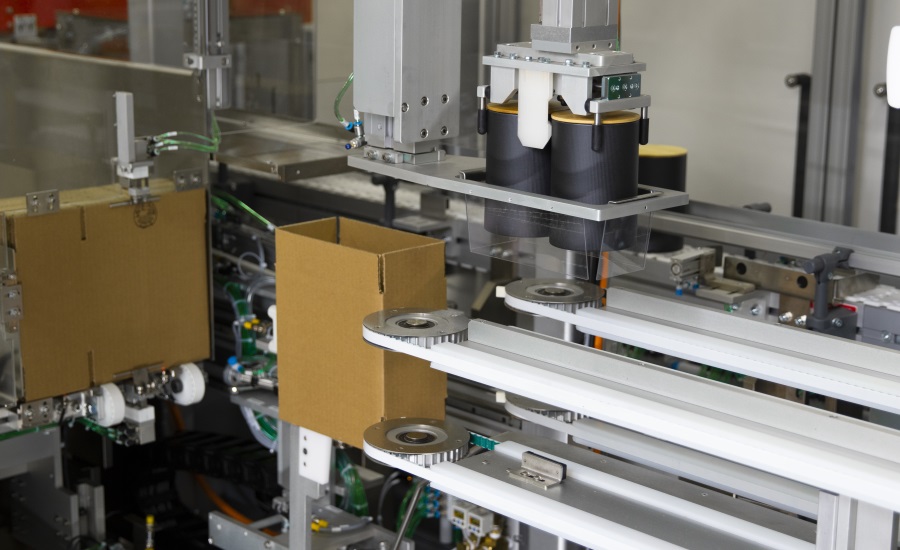
MGS announced in May the release of its new Matrix TL top-loading case packer. Courtesy of Packsize
MGS, a global leader in packaging automation solutions, announced in May the release of its new Matrix TL top-loading case packer. For packaging facilities with low-to-medium production rate requirements and diverse packaging requirements, the Matrix TL offers a complete form, fill and seal case packing solution with a small footprint, competitive rate of speed and quick changeovers.
Market demand for variety and more sustainable formats is challenging manufacturers, with the proliferation of stock keeping units (SKUs), product types and packaging configurations – from specialty and seasonal packaging to different case sizes and formats for wholesalers or convenience stores. Satisfying such a wide array of consumer and retailer demands means frequent equipment changeovers to accommodate different packaging runs and having a large quantity of products and materials at hand, which take up valuable facility space.
The Matrix TL case packer easily handles the unique specifications of diverse packaging runs with speed and efficiency. It offers an effective solution for a large range of applications and product types, including Home Care, Personal Care, Pharma and Med Device, and works as a secondary packaging solution for Food and Beverage products like bottled or canned foods and drinks.
Ishida Europe Releases New Version of Automatic Case Packing System
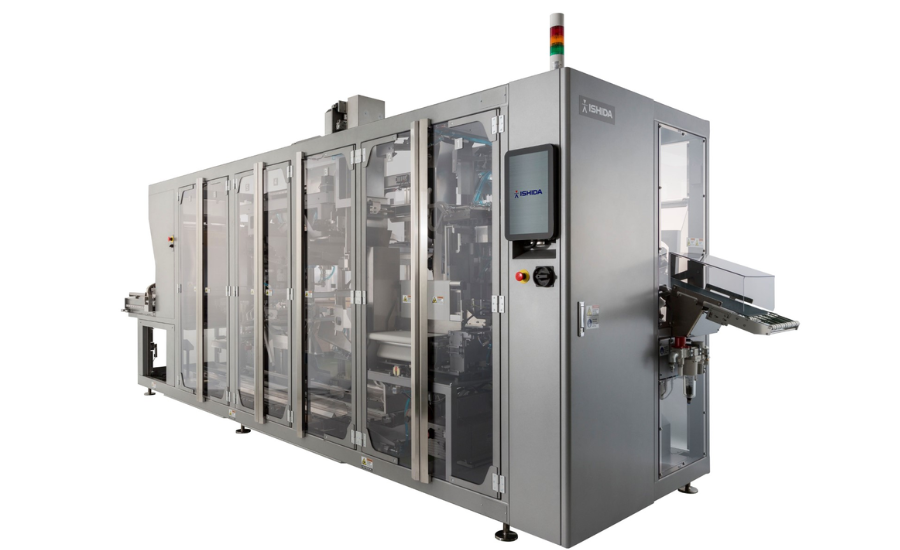
Ishida Europe announced in September the launch of a new version of its ACP-700 series automatic case packing system (ACP) for snacks and other dry product packs – the ACP-722 RRP. Courtesy of Ishida Europe
Ishida Europe announced in September the launch of a new version of its ACP-700 series automatic case packing system (ACP) for snacks and other dry product packs, offering a fast, flexible and highly compact solution for a wide range of bag and case sizes and pack patterns.
The ACP-722 RRP offers one of the smallest footprints currently available, being up to 50% smaller than equivalent casepacker models. As well as saving valuable factory space, this also allows quick and easy installation and seamless integration into existing production lines. The single directional flow design produces a lean and compact line layout which can also easily accommodate twin lines. Top speed is 20 cases per minute.
Key to the machine’s small size is the combination of case infeed and alignment, bag sorting and packing as well as case closing and sealing in one single compact unit, removing the need for additional conveyors. This also means that all functions can be controlled from one HMI touch screen. Product changeover is initiated at the touch of a button. This process is completely automatic and performed in under three minutes, without requiring a skilled technician.