
All Images Courtesy of NOVA Chemicals.
New Technology Optimizes Coextrusion Films for Fresh Produce Packaging
When it comes to package design, fresh produce films require a specific balance of properties to protect the food and preserve freshness for as long as possible. Fruits, vegetables, and leaves are living tissues which continue to respire after harvesting.
To maintain optimal freshness in these applications, oxygen, carbon dioxide and moisture must be able to permeate through the packaging film at specific rates. Film clarity is another important factor as consumers value visual appeal and aesthetics when purchasing fresh foods. Finally, produce packaging needs sufficient durability for high-speed converting and to ensure the produce is protected during storage and transportation.
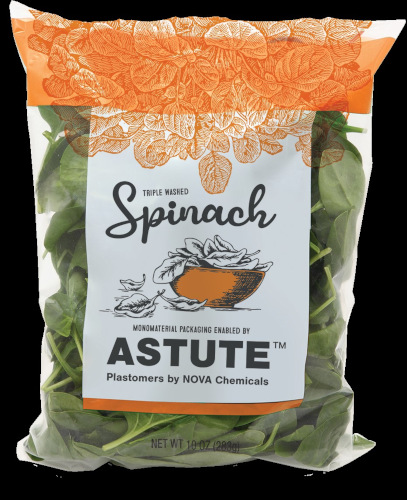
Blends of polyethylene- based plastomers (very low-density linear polymers) with linear low density (LLDPE) polyethylenes are often used in produce films to achieve the optimal combination of breathability, optics, and stiffness. NOVA Chemicals has recently developed a new polyethylene (PE) brand, ASTUTE™ plastomers, that includes ASTUTE QHsK908 resins and delivers high performance in many flexible film and packaging applications.
ASTUTE QHsK908 resins were designed to provide equivalent or better film performance than Plastomer + LLDPE blends. Testing at NOVA Chemicals showed that blown films containing ASTUTE QHsK908 plastomers provided up to 25% higher oxygen transmission rates (OTR), while also delivering improved clarity, stiffness and durability when processed under specific conditions. These improvements make this new resin an excellent candidate for use in films for fresh produce packaging.
Packaging Strategies sat down with NOVA Chemicals to discuss the results of their recent blend study that compared ASTUTE QHsK908 resins to Plastomer + LLDPE blends. We talked to Dan Ward, Specialist, Technical Service, and Brian Molloy, Specialist, Application Development.
PS: What are some of the challenges in designing fresh produce packaging?
DAN: Fresh produce packaging needs to have specific permeabilities to extend product shelf life and maintain freshness. To achieve this, highly permeable plastomers or very low density polyethylenes are essential components of coex layers.
However, many plastomers are prone to pellet agglomeration, film blocking when coextruded in an outside layer as well as reducing physical properties such as tensile strength or stiffness. To mitigate these challenges, plastomers are often blended with higher density LLDPE resins. Manufacturers can often “dial-in” a specific permeability by changing the LLDPE/Plastomer blend ratio, but simultaneously meeting permeability, optical and film tensile properties when using plastomer blends in coex films can be challenging.
ASTUTE QHsK908 resins are a new intermediate density plastomer resin that provides an optimal combination of properties which overcomes challenges of Plastomer + LLDPE blends in fresh produce packaging. It was designed to provide excellent film physical, optical and seal properties. In recent studies, we also found QHsK908 can provide high permeabilities in blown films run under certain conditions.
PS: What materials were tested in the blend study?
BRIAN: Our study compared the performance of monolayer blown films made from NOVA Chemicals’ ASTUTE QHsK908 plastomer and SCLAIR® FP120 LLDPE resin against blends of plastomer and LLDPE.
- Three blends were tested for oxygen transmission rates (OTR) as well as physical performance via dart impact resistance and tear tests.
- NOVA Chemicals’ SCLAIR FP120, a performance film resin, was also run as a control.
- ASTUTE QHsK908 plastomers blended with 30 percent 0.902 density plastomer blend was also tested for OTR at 0.5 mil and 1 mil thicknesses.
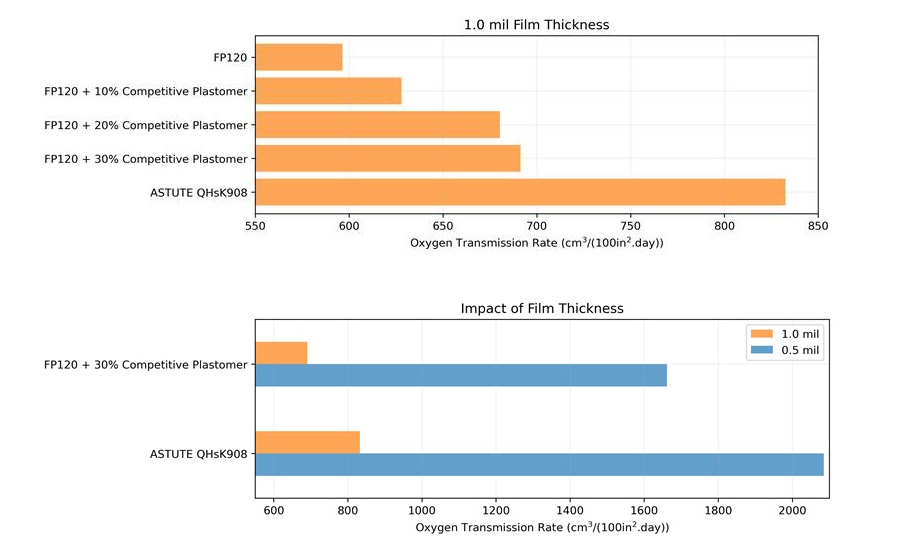
PS: How did ASTUTE QHsK908 plastomers perform against other plastomer blends?
DAN: ASTUTE QHsK908 plastomers displayed significantly higher OTR than all other films in the study. The 0.5 mil film, made from ASTUTE QHsK908 plastomers, had an OTR of more than 2,000 cm³/100in²/day – over 25 percent greater than competitive alternatives such as the 0.5 mil 0.902 density plastomer blend. The single layer of ASTUTE QHsK908 resins also showed a much higher dart impact resistance than the plastomer blends, highlighting that the film not only provides breathability but is also tough enough to withstand high-speed converting and transportation.
PS: How do ASTUTE QHsK908 plastomers achieve this combination of properties?
DAN: Produced with NOVA Chemicals’ Advanced SCLAIRTECH™ Technology, ASTUTE QHsK908 plastomers have a unique resin architecture. This architecture allows for higher permeability when QHsK908 in blown films is processed under conditions of relatively high draw ratios and short process times.
PS: What are the processing advantages of ASTUTE QHsK908?
BRIAN: ASTUTE QHsK908 plastomers can be used to create highly breathable films and optimize overall packaging performance. It can replace plastomer blends to simplify production processes and enable source reduction through downgauging and lower costs. The benefits of using an QHsK908 in all-PE coex structures create possibilities for enhanced functionality that supports sustainability initiatives and helps reduce plastic waste.
PS: How can more effective breathable films contribute to sustainability goals?
BRIAN: According to the United Nations Environment Programme (UNEP) Food Waste Index Report 2024, food waste is responsible for an estimated 8 to 10 percent of global greenhouse gas emissions. Food spoilage is a major factor that contributes to food waste. By better control of and/or increasing the OTR of produce films, we can extend produce shelf life and reduce waste. Higher performing resins like ASTUTE QHsK908 plastomers can also help film manufacturers to meet other performance requirements with thinner films, thereby reducing the overall package weight.
The needs of fresh produce packaging are complex. ASTUTE QHsK908 plastomers deliver a permeable film solution without the processing challenges that accompany lower density resins. NOVA Chemicals’ QHsK908 offers the ideal combination of OTR, stiffness, excellent optical properties, and durability to meet demanding standards for produce and other flexible packaging. Manufacturers can benefit from simplified processes and downgauged structures while providing consumers with sustainable packaging that extends the shelf life of their fresh food purchases.