
Image courtesy of Dematic
Palletizing, depalletizing equipment drives efficiencies in warehouses
Rise in co-packing and sustainability goals impact equipment.
For organizing company The Home Edit, one of the most iconic aspects of their methods is their rainbow organization process for foods, clothing, books and more. The result is a visually organized display to help finding things and putting them away in one’s home, school or office.
In beverage warehouses, the influx of SKUs and the rise of mixed pallets has prompted operations to turn to semi-automated and automated palletizing and depalletizing solutions to support the organization and execution of distributing these products.
“There certainly has been an increased interest in ergonomic semi-automated palletizers in the last several years, as well as an interest in depalletizing especially as this equipment is used to feed dispensing and case storage type systems,” says Paul Laman, vice president of sales of beverage at DMW&H, Fairfield, NJ.
“Much of the growth in ergonomic palletizing has been coming from the beverage industry due to the increasing need for pallet loads of mix SKUs,” Laman explains.
Ted Yeigh, NW region sales and palletizer division marketing manager at Columbia Machine Inc., Vancouver, WA, describes the palletizing market as very buoyant among food and beverage players. Although he notes there has been some softening post COVID, Columbia Machine still has seen strong performance. This is prompted by the increased productivity that palletizers can offer, he says.
Kyle Nevenhoven, head of solution consulting at Dematic, Atlanta, also highlights the efficiencies that can be realized through the use of automated and semi-automated depalletizing equipment.
“Depalletizers in beverage distribution, whether automated or ergonomic, represent a very efficient way of replenishing automated case buffer systems with the inventory needed to fulfill outbound orders,” he says. “Palletizers offer the ability to palletize complex loads very efficiently. Ergonomic palletizing systems can take a sequenced or semi-sequenced flow of cartons and palletize them very rapidly to create a dense and stable pallet.
“Automated palletizing allows for the full automation of the pallet-building process, achieving the same outcome as ergonomic palletizing with little human intervention,” Nevenhoven continues. “Beyond labor savings in distribution centers, intelligent software is key to unlocking the full benefit of these technologies, building pallet configurations that consider case size, stackability, store aisle sequences, and even reverse stop sequence requirements for multi-stop pallets.”
Beyond labor challenges, he notes that SKU proliferation and innovative packaging types have impacted pallet complexity.
Meanwhile, Columbia Machine’s Yeigh highlights that the growth of co-packing operations is prompting the need for palletizing solutions to support the constant changeovers within those operations.
“I think there’s more and more co-packing … which what that means is more and more changeovers,” he explains. “Sometimes the packaging format doesn’t changeover, but the controls need to be able to decipher whether its product A, product B, product C, whatever you’re running, so warehouse management systems and ERPs and inventory tracking can all be kept accurate and really those changeovers need to be almost real time.
“Columbia has numerous palletizers that have zero time, zero tools and zero person input to changeovers and the changeover can be instantaneous,” Yeigh continues. “That leads into productivity.”
Machinery help wanted
For management personnel in beverage warehouses, they understand the impact that labor shortages has had on operations. Although there are limits to how operations and distribution managers can address labor shortages, the automated and semi-automated solutions of palletizers and depalletizers are a solution more beverage warehouses are turning to.
Columbia Machines’ Yeigh summarizes these as, “if you can’t find the labor, you have to automate.”
With this, Yeigh explains that personnel trained on lift trucks and other machinery still serve an important role in the warehouse, but they also can be trained as a line operator or delivering empty pallets into system as well as many other roles beyond the physical demands that come with manual pallet building.
DMW&H’s Laman adds that with the adoption of palletizing systems, operations can address their labor challenges while improving productivity.
“Considering the current labor shortages, automation of this less desirable labor component is valuable. Even with semi-automated palletizing, the productivity rate is three-times higher than traditional manual palletizing,” he says.
Dematic’s Nevenhoven also highlights the impact that labor shortages has had on the adoption of palletizing and depalletizing equipment in beverage operations.
“Labor shortages are the most impactful factor driving the use of palletizing and depalletizing automation in beverage distribution,” he says.
By implementing these solutions, warehouses can increase efficiency.
“Depalletizing can offer efficiency in the distribution center, as it is well suited to the replenishment of automated or semi-automated pallet-building solutions,” Nevenhoven says. “Palletizers, particularly those that can build complex mixed-case pallets, are the single technology that can be adopted by beverage distributors to impact the entire distribution process. From increasing efficiency in the distribution center to creating more stable and better-organized pallets for transportation and delivery, as well as enabling more timely and effective merchandising at retail due to sequenced and store-friendly pallets, a true end-to-end efficiency gain can be realized.”
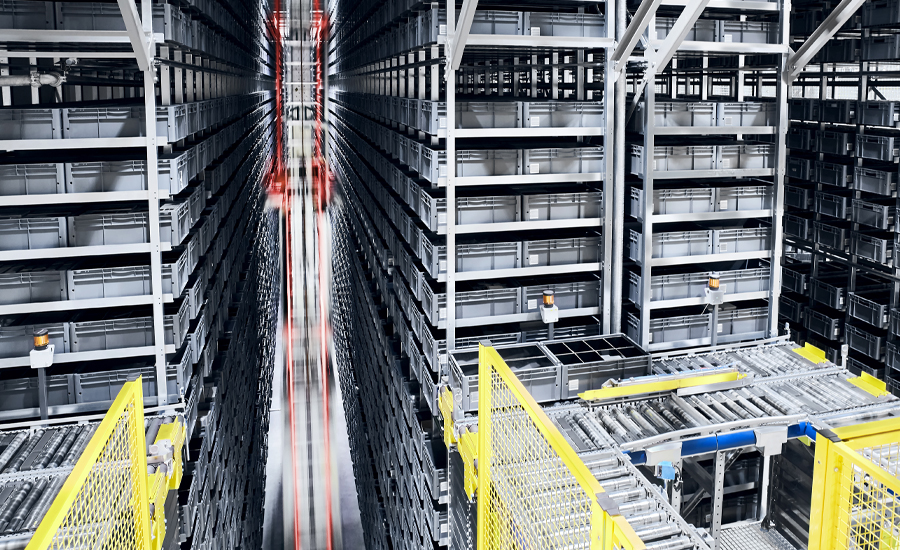
Sustainability factors
With sustainability a key topic in the beverage market, much attention is directed toward the primary and secondary packaging materials. However, experts note that original equipment manufacturers also are taking this into consideration with today’s palletizing solutions.
Columbia Machine’s Yeigh explains that as beverage manufacturers reduce or eliminate packaging materials, it is important to support those changes. As an example, he points to a six-pack of relatively small bottles that might be looking to reduce or eliminate a tray and use only a shrink overwrap. Yeigh highlights that Columbia Machine has developed different features on its palletizing equipment to support that.
“You need a machine that will not put undue stress or impact on packaging as it goes through the palletizing process to mare the product if you will or damage the product and then it becomes unsaleable,” Yeigh says.
Another example would be glass bottles. “[T]o reduce carbon footprint, feeding into sustainability, and just cost, producing cases of glass bottles with no dividers is something we see more and more often,” Yeigh says, “and Columbia has solutions that we have for extremely gentle product handling to accommodate that.”
Getting ‘smarter’
Although many might dub palletizing and depalletizing equipment as a next generation solution, original equipment manufacturers see more potential to take these solutions to the next level.
“Artificial intelligence (AI) continues to advance in the material handling space, and its impact on operations continues to grow,” Dematic’s Nevenhoven says. “Machine learning introduces the concept of understanding SKU attributes by automatically capturing all pertinent information, reducing the manual teach-in processes needed for the successful use of highly automated palletizing and depalletizing equipment.
“For depalletizers and palletizers, artificial intelligence has the potential to increase tolerances while reducing downtime, as AI-based software applications can better identify when a fault or error impacts system operation,” he continues. “When an issue does not affect the safe operation of the equipment, human intervention can be avoided.”
Columbia Machine’s Yeigh explains that in order for AI to be valuable, you need a massive amount of data to mine that information and generate useful feedback.
“When you make custom equipment, custom solutions, it’s harder to build that massive amount data for the data and the feedback to be granular enough to be really useful, but the technologies all there,” he explains.
As an example, Yeigh notes that with the right sensors and HMI interface, AI could detect anomalies on a component and alert an operator about a potential issue that could result in downtime if not addressed. He adds that AI could even go further down the line to check inventory for spare parts for a potential issue on the horizon, alerting the team to purchase low-inventory parts.
DMW&H’s Laman notes that it’s not so much AI but building on the intelligence that already is part of palletizing and depalletizing.
“Not necessarily AI, but smart palletizing and waving parameters following mature business intelligence rules allows for optimally configured pallets which allows for more efficient delivery and put-away when received at the retailer,” he says.